A gas line near the alley was moved to clear a path for a larger driveway. The line was pressure tested and did not pass the test. Four leaks were found in the attic. The week before, workman were in the attic installing a vent-a-hood were exposed to the leaking gas. The good news is there was no hot work going to that could have been disastrous.
Confined Space
A confined space that contains certain hazardous conditions may be considered a permit-required confined space under the standard. Permit-required confined spaces can be immediately dangerous to workers’ lives if not properly identified, evaluated, tested and controlled. A permit-required confined space means a confined space that has one or more of the following characteristics:
-
- Contains or has the potential to contain a hazardous atmosphere
- Contains a material that has the potential for engulfing an entrant
- Has an internal configuration such that an entrant could be trapped or asphyxiated by inwardly converging walls or by a floor which slopes downward and tapers to a smaller cross-section
- Contains any other recognized serious safety or health hazard
Determining Confined Space or Permit Required
Before beginning work on a residential homebuilding project, each employer must ensure that a competent person identifies all confined spaces in which one or more employees work. They must also identify each space is a permit-required.
The competent person does not have to physically examine each attic, basement or crawl space, provided that the competent person can reliably determine whether the spaces with the same or similar configuration contain a hazard or potential hazard that would require the permit-space classification.
The initial evaluation may be done using existing experience and knowledge of the space by the competent person and does not need to be documented. A competent person responsible for inspecting new homes being built to identical specifications with the same materials need not physically inspect each attic separately to determine if it is a permit-required confined space.
How Spaces in Residences are Impacted
Spaces in a residential home may be considered confined spaces or permit-required confined spaces during the construction or remodeling process. The vast majority of the standard’s requirements only apply to permit-required confined spaces, and attics, basements, and crawl spaces in a residential home — three common spaces – will not necessarily trigger these requirements.
Attics
Attics will not be considered a confined space because there is not limited or restricted means for entry and exit unless there is a hazard. Access is the biggest determining factor for example, pull down stairs that resemble the structure of a stationary stairway and do not require an employee to ascend /descend hand-over-hand would not be considered a confined space if there are no impediments to egress. A scuttle hole would be limited access.
Attics that are determined to be confined spaces would generally not be permit-required confined spaces because they typically do not contain the types of hazards or potential hazards that make a confined space a permit-required confined space. But, has leaks, extreme heat in an attic can be considered a serious physical hazard such that the attic could be considered permit-required confined space.
Basements
Basements in a residential home that are designed for continuous occupancy by a homeowner are not considered confined spaces under the standard, provided the basement is configured as designed (e.g., has permanent stairs, a walk-out entry/exit, or an egress window installed).
Crawl Spaces
Crawl spaces in a residential home will not typically trigger the majority of the requirements of the standard unless they contain a physical hazard such as an exposed active electric wire.
Regardless of the area, the competent person needs to assess acute health hazards that may be present when assessing confined spaces, such as toxic (carbon monoxide), flammable, or explosive atmospheres. Safety Data Sheets (SDSs) must be maintained and reviewed to fully assess potential hazards prior to worker entry into a confined space to determine whether it is a permit-required space.
Employers Obligations
Host Employer
The employer who owns or manages the property where the construction work is taking place.
Controlling Contractor
The employer who has overall responsibility for construction at the worksite (note that if the controlling contractor owns or manages the property, then it is both a controlling employer and a host employer).
Entry Employer (Sub Contractor)
Any employer who decides that an employee it directs will enter a permit-required confined space. The standard makes the controlling contractor the primary point of
contact for information about permit-required confined spaces at the work site. The controlling contractor passes information it has about permit-required confined spaces at the work site on to the employers whose workers will enter the spaces (entry employers).
Entry Employer
Entry employers must give the controlling contractor information about their entry program and hazards they encounter in the space, and the controlling contractor passes that information on to other entry employers. The controlling contractor is also responsible for making sure that employers outside a space know not to create hazards in the space, and that workers from different entry employers working in a space at the same time do not create hazards for each other.
Host/Controlling Employer
Before entry operations begin, a host employer with the following information must provide it to the controlling contractor:
-
- Location of each known permit-required confined space
- Hazards or potential hazards in each space or the reason it is a permit-required confined space
- Any precautions that the host employer or any previous controlling contractor/entry employer implemented for the protection of workers in the permit-required confined space
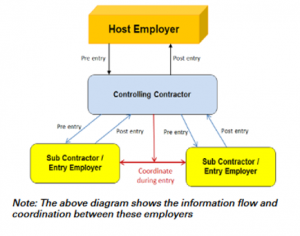
The multi-employer communication requirements only apply to host employers with employees who work at the worksite, regardless of when those workers are at the site and only apply to permit-required confined spaces. In addition, beyond this duties discussed above, host employers and controlling contractors are not responsible for compliance with the permit-required confined space program provisions of the standard if they have no reason to anticipate that the employees they direct will enter a permit-required confined space.
Entry Employer Obligations
Informing employees if they are working in the vicinity of each space of the location and danger posed by that space. This can be done by posting and positioning warning signs at each possible point of entry, or by other equally effective means.
The employer must also either take steps to prevent its employees from entering that space or ensure that entry only occurs through a permit program or as otherwise allowed by the standard (alternative entry procedures).
Employers must attempt to eliminate or isolate the hazards in the space. Engineering (ventilating) and work-practice controls (schedules, rotations) must be in place and finally, appropriate Personal Protective Equipment (PPE) is required if allowing an employee to enter a permit space.
Training on the space, the existence and location of, and dangers posed by, each permit-required confined space, and that they may not enter such spaces without authorization. Entry employers must train workers involved in permit-required confined space operations so that they can perform their duties safely and understand the hazards in permit spaces and the methods used to isolate, control or protect workers. Workers not authorized to perform entry rescues must be trained on the dangers of attempting such rescues.
The permit-required confined space program must establish a system for preparing, using, and canceling entry permits, which are written or printed documents that allow and control entry into permit spaces.
Entry employers must ensure that properly trained rescue and emergency services are available before entry into permit-required confined spaces. For a full discussion of an entry employer’s obligations to provide rescue, see OSHA’s Fact Sheet entitled: is 911 your Confined Space Rescue Plan.