Introduction to OSHA Compliance
Understanding OSHA: Purpose and Background
The foundation of the Occupational Safety and Health Administration (OSHA) is deeply rooted in promoting and ensuring worker safety. Born from the vital principles of the Occupational Safety and Health Act, OSHA’s key objective is to mitigate the hazards that employees face in their daily work environments.
Embracing OSHA compliance is a collaborative endeavor. It requires a concerted effort from both employers and their teams to deeply understand and rigorously apply safety measures. This joint commitment is essential in nurturing an environment where safety is not just a regulation, but a shared value.
Need OSHA Help? Our OSHA Courses.
The Importance of OSHA Compliance for Businesses
Embracing OSHA compliance is crucial for businesses, transcending mere legal obligations. It’s about establishing a safe and secure work environment, which is central to the health and morale of employees. This proactive approach to safety helps minimize the occurrence of work-related injuries and health issues, contributing to a more dynamic and productive workplace.
Further, adherence to OSHA standards reinforces a business’s dedication to its workforce. This dedication is reflected in the trust and loyalty of employees, who, when working in a safe environment, are likely to be more engaged and effective. Moreover, a reputation for safety can elevate a company’s standing, attracting quality talent and fostering positive relationships with clients and partners.
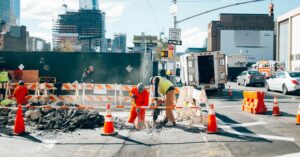
Key Components of OSHA Compliance
Workplace Safety Standards and Regulations
Delving into OSHA’s detailed safety standards and regulations is essential for fostering a secure work environment. These guidelines act as a blueprint for pinpointing and neutralizing various risks inherent in diverse work settings. They span from overarching safety protocols to specific rules for handling dangerous materials, ensuring comprehensive coverage of workplace safety issues.
Adopting these standards is integral to protecting employees from workplace dangers. This commitment includes the correct application of safety gear and the development of robust hazard communication strategies. By keeping up-to-date with OSHA’s ever-evolving regulations, companies can not only sidestep legal repercussions but also cultivate a safer, more efficient workplace atmosphere.
Furthermore, consistent training in these safety regulations is paramount. It’s important for every employee, regardless of their role, to receive regular instruction on relevant safety measures. This continuous learning process is key to adapting to new safety standards and effectively addressing new challenges in maintaining workplace safety.
Training Requirements and Best Practices
OSHA compliance hinges significantly on the quality of training provided to employees. Varied across industries and job roles, these training programs are designed to impart a deep understanding of safety risks and the competencies to address them. This encompasses educating employees about the correct use of safety equipment, emergency response actions, and identifying potential hazards.
Advanced training approaches exceed standard protocols by incorporating interactive and engaging learning techniques that resonate with diverse learning preferences. It’s also crucial to conduct regular update sessions, ensuring that employees are abreast of evolving safety practices and standards. Practical, scenario-based training exercises further deepen employees’ grasp of safety measures.
In addition to delivering quality training, meticulous record-keeping of all training activities is vital. These records not only demonstrate adherence to OSHA guidelines but are also crucial during audits or inspections. They provide a framework for evaluating and continuously enhancing the safety training program.
Support Needed? Contact Us.
Record Keeping and Reporting Obligations
Adhering to OSHA’s comprehensive record keeping and reporting rules is pivotal for any business committed to workplace safety. Keeping detailed records of all workplace injuries and illnesses is not just a regulatory formality. It’s an essential part of a company’s safety strategy, providing invaluable insights into the effectiveness of current safety practices and highlighting areas needing attention.
In these records, it’s important to meticulously document the specifics of each incident, such as the time, location, and the employees involved. Regular analysis of this data is crucial for spotting safety trends and potential risks, enabling proactive measures to mitigate similar incidents in the future.
Additionally, OSHA mandates the timely reporting of certain severe incidents, like hospitalizations or severe injuries. This requirement is not only about fulfilling a legal obligation but also about facilitating OSHA’s role in providing necessary support, including conducting site inspections or offering targeted safety recommendations.
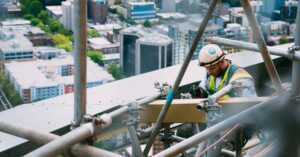
Steps to Achieve OSHA Compliance
Conducting a Workplace Hazard Assessment
A crucial element in maintaining OSHA compliance is the execution of a comprehensive workplace hazard assessment. This process involves a detailed examination of the work environment to pinpoint potential sources of injury or illness. It’s important to look beyond the obvious dangers, identifying subtler risks that might otherwise go unnoticed.
Involving employees from various levels and departments in this assessment is key. Those who are on the front lines often have unique insights into potential dangers in their specific work areas. This inclusive approach ensures a more thorough and accurate detection of hazards.
After identifying the risks, the next step is to classify them based on severity and likelihood. Addressing the most pressing hazards first allows for a more effective use of resources in enhancing safety measures. Additionally, continual re-evaluation of the workplace is important, as new hazards can arise with changes in operations, technology, or staff.
Implementing Safety Programs and Controls
After identifying hazards through a thorough assessment, the next critical step is implementing robust safety programs and controls. This involves developing and executing strategies that effectively mitigate identified risks. A well-designed safety program is comprehensive, addressing various aspects of workplace safety, from emergency response procedures to daily operational safety protocols.
Key to these programs is the integration of effective control measures. These can range from engineering controls, like redesigning equipment or workspace to minimize hazards, to administrative controls, such as altering work schedules or procedures to reduce risk exposure. Personal protective equipment (PPE) also plays a crucial role, especially in situations where hazards cannot be completely eliminated.
Regular monitoring and evaluation of these safety programs are essential to ensure their effectiveness. This process includes gathering feedback from employees, analyzing safety data, and making adjustments as necessary. Continuously improving these safety programs helps to adapt to new challenges and maintain a high standard of workplace safety.
Employee Training and Education Strategies
Crafting and implementing tailored training and education programs is essential for achieving OSHA compliance and enhancing workplace safety. These programs must be designed to address the unique aspects of the workplace and the varied roles of its employees. The aim is for each employee to gain a comprehensive understanding of the safety procedures relevant to their work and how to effectively implement them.
Utilizing dynamic and interactive training approaches is crucial for engaging employees and reinforcing learning. Incorporating practical exercises, simulated emergency scenarios, and innovative digital training methods can significantly boost the effectiveness of these sessions. Periodic training, complemented by unannounced drills, ensures ongoing awareness and readiness for potential emergencies.
In addition, the ever-changing nature of the workplace necessitates ongoing education. Employees should regularly receive updates and refresher training to stay aligned with evolving safety regulations, technological advancements, and procedural changes. Encouraging employee participation in creating training content can also foster a deeper connection to and understanding of safety protocols.
Common Challenges in OSHA Compliance
Identifying and Overcoming Compliance Obstacles
Navigating the path to complete OSHA compliance can be fraught with challenges. Key among these are the limited understanding of the breadth of OSHA rules, constrained resources for enacting safety measures, and a workforce sometimes hesitant to adapt to new safety protocols.
A pivotal step in surmounting these hurdles is thorough education on OSHA’s guidelines. This might involve participating in industry-specific safety training, seeking advice from safety compliance professionals, or exploring extensive online educational materials. Equally important is the dedication of adequate resources—financial, human, and technological—to ensure the successful deployment of safety initiatives.
Cultivating a safety-centric culture is another vital element. This requires buy-in at every level of the organization, from executives to entry-level workers. Promoting transparent communication about safety issues, rewarding adherence to safety practices, and leadership that exemplifies a commitment to safety can collectively help in overcoming resistance and ingraining a culture where safety is a priority.
Addressing Common Workplace Safety Violations
Dealing with common workplace safety violations is a critical aspect of maintaining OSHA compliance. These violations can range from inadequate fall protection in construction sites to insufficient hazard communication in general industry settings. Understanding these common violations and their implications is essential for employers to ensure a safe workplace and avoid OSHA citations.
To address these issues, employers must first conduct a thorough review of their current safety protocols against OSHA standards. This includes examining areas like personal protective equipment usage, employee training effectiveness, and workplace hazard identification. Regular safety audits can help identify lapses in compliance and provide opportunities for improvement.
Implementing corrective measures is the next crucial step. This might involve updating safety equipment, enhancing employee training programs, or revising operational procedures to mitigate identified risks. Engaging employees in this process, through safety training and open discussions about workplace hazards, can lead to more effective solutions and a collective commitment to safety.
OSHA Compliance for Specific Industries
Industry-Specific Safety Standards
Adapting to the unique safety requirements of different industries is a key component of comprehensive OSHA compliance. Each industry presents distinct safety challenges, necessitating specialized regulations. For example, the construction industry heavily focuses on fall prevention, while manufacturing might prioritize safeguards against machinery hazards.
Businesses must thoroughly understand and implement the OSHA guidelines that are pertinent to their specific industry. This could range from managing exposure to hazardous substances in sectors like healthcare and chemical processing, to enforcing rigorous fire safety protocols in the hospitality and retail industries. These standards are meticulously crafted to mitigate the particular risks inherent in various work settings.
Keeping pace with changes in these industry-specific OSHA standards is also critical. As technological innovations emerge and new health and safety research comes to light, OSHA updates its regulations to better protect workers. Employers must remain vigilant, regularly reviewing and updating their safety strategies to align with the latest standards, thereby enhancing the safety and well-being of their employees.
The Role of Technology in Ensuring OSHA Compliance
Innovative Tools for Safety Management
The integration of cutting-edge technologies has significantly elevated the standards of workplace safety and OSHA compliance. Modern safety management has been transformed by the advent of sophisticated software that simplifies the tracking, reporting, and analysis of safety data. These digital tools enable more effective identification of risk patterns and foster data-driven decision-making in safety protocols.
Emerging wearable technologies, like sensor-laden safety gear, are revolutionizing risk management in hazardous work environments. These advanced devices can monitor environmental conditions, track worker health indicators, and provide immediate alerts in critical situations, greatly enhancing the safety of employees in fields like construction and industrial manufacturing.
Virtual reality (VR) is also making a profound impact on safety training. By simulating realistic workplace scenarios, VR allows employees to navigate potential hazards in a risk-free virtual setting. This immersive approach not only deepens understanding of safety procedures but also equips workers with practical experience in handling real-world safety challenges.
These innovative advancements are reshaping the approach to safety management, offering smarter, more proactive solutions for maintaining OSHA compliance and ensuring a safer work environment.
The Impact of Digital Record Keeping
Transitioning to digital record keeping systems has revolutionized the way businesses approach OSHA compliance and safety management. These digital solutions offer a streamlined, precise method for maintaining critical safety documentation. From incident reports to training records and compliance certificates, digital record keeping ensures all vital data is organized and easily accessible.
A major advantage of this digital shift is the enhanced capability for data analysis. Safety professionals can swiftly sift through digital records to spot trends and recurring issues in workplace safety, allowing for more effective preventive strategies. This analytical edge provided by digital systems is pivotal in crafting targeted safety interventions.
Digital record keeping also brings a new level of transparency and readiness in compliance matters. It simplifies the process of showcasing a company’s safety diligence during regulatory audits or inspections. Moreover, in the case of an incident, having detailed digital records readily available streamlines the response and investigation, aiding in swift resolution and analysis.
Legal Implications of Non-Compliance
Penalties and Fines Associated with OSHA Violations
Understanding the penalties and fines associated with OSHA violations is crucial for businesses. Non-compliance can result in significant financial consequences, which vary based on the severity and nature of the violation. For minor infractions, penalties may be more lenient, but serious violations, especially those resulting in injury or death, can lead to substantial fines.
Repeated or willful violations are treated even more stringently. OSHA categorizes these as instances where employers knowingly fail to comply or show indifference to employee safety. Such violations can result in fines amounting to tens or even hundreds of thousands of dollars, depending on the specifics of the case.
Beyond financial penalties, OSHA violations can also damage a company’s reputation and lead to increased scrutiny in future inspections. This underscores the importance of not only understanding OSHA regulations but also rigorously implementing them to ensure workplace safety and avoid these costly penalties.
Legal Cases and Precedents in OSHA Enforcement
Historical legal cases play a pivotal role in shaping the enforcement and interpretation of OSHA regulations. These cases often stem from serious workplace incidents, where non-compliance with safety standards has led to accidents or fatalities. Examples include cases related to insufficient safety measures in high-risk work environments or failure to adhere to chemical safety regulations, which have had significant legal repercussions.
The outcomes of these legal battles serve as crucial learning points for employers. They underscore the legal mandate to ensure a safe workplace and the severe implications of neglecting this responsibility. The aftermath of these cases frequently results in more rigorous enforcement of OSHA guidelines and occasionally leads to the introduction of new safety regulations.
These cases also highlight the necessity for continuous hazard evaluation and immediate action on identified risks. Employers can use these legal precedents to better comprehend their obligations and the serious consequences of failing to meet them.
Staying Updated with OSHA Regulations
Resources for Keeping Up with Regulatory Changes
Staying informed about regulatory changes in OSHA standards is essential for businesses to ensure ongoing compliance and workplace safety. Several resources are available to assist in this endeavor. OSHA’s official website is a primary source, offering up-to-date information on regulations, guidance documents, and training resources. Regularly visiting this site can keep businesses informed about the latest changes in safety standards.
Trade associations and industry groups also play a vital role in disseminating information about OSHA updates. These organizations often provide sector-specific insights and can be valuable resources for understanding how new regulations might impact specific industries. They may offer seminars, webinars, and newsletters focused on regulatory changes and best practices in compliance.
Additionally, subscribing to safety journals, attending safety conferences, and engaging with online forums dedicated to occupational safety can provide a broader perspective on emerging trends and changes in OSHA regulations. Employing these resources effectively ensures that businesses remain knowledgeable and compliant with the latest OSHA requirements.
Tips for Ongoing Compliance and Safety Improvement
Ensuring continuous adherence to OSHA standards and enhancing workplace safety is an ongoing process. Here are several key strategies for achieving this:
Periodic Safety Evaluations or Mock Inspections: Regular evaluations of the workplace for safety hazards are crucial. These assessments help in uncovering and rectifying compliance gaps and potential risks in a timely manner.
Consistent Training and Employee Involvement: Continuous education and involvement of employees in safety practices are essential. Facilitating open forums for safety discussions and encouraging employees to report safety issues can cultivate a proactive safety culture.
Keeping Abreast of OSHA Updates: Staying informed about the latest OSHA updates is key. Leveraging online resources, industry-specific publications, and joining professional safety organizations can be beneficial in keeping track of regulatory developments.
Effective Safety Concern Reporting Mechanisms: Establishing an easy and confidential system for reporting safety concerns is important. This allows employees to report potential risks without fear, leading to quicker resolution of safety issues.
Adoption of Modern Safety Technologies: Investing in the latest safety technologies and ensuring proper maintenance of safety equipment can greatly enhance overall safety standards.
Leadership Commitment to Safety: A commitment from the management towards safety sets a tone for the entire organization. When leaders actively promote and participate in safety initiatives, it embeds a safety-first mindset across all operations.
Regular Safety Policy Reviews: Continually reviewing and updating safety policies to align with current workplace scenarios and OSHA standards is vital for maintaining effective safety protocols.
Adopting these measures not only helps in complying with OSHA regulations but also builds a safer and more efficient workplace environment.
Conclusion: The Future of Workplace Safety and OSHA Compliance
Emerging Trends in Workplace Safety
The landscape of workplace safety is continuously evolving, introducing new trends and practices. A prominent development is the integration of advanced analytics and artificial intelligence (AI) in identifying and mitigating safety risks. These technologies enable a predictive approach, using data analysis to foresee and prevent potential incidents.
There’s also a growing recognition of the importance of mental health as a component of workplace safety. Companies are increasingly adopting measures to support employees’ mental well-being, incorporating initiatives like stress reduction programs and flexible work arrangements.
With the shift towards remote and hybrid work models, safety protocols are adapting to these new work environments. This includes addressing not just physical health, but also factors like digital security and home office ergonomics.
Environmental consciousness is also shaping workplace safety trends. More businesses are moving towards sustainable safety practices, such as using eco-friendly safety equipment and implementing measures to minimize environmental hazards.
These trends reflect a comprehensive view of workplace safety, extending from physical hazards to mental health and environmental sustainability, showcasing an all-encompassing approach to employee well-being.
The Evolving Landscape of OSHA Compliance
OSHA compliance is an ever-changing field, shaped by emerging workplace trends and technological innovations. A significant shift in recent years is the move towards anticipatory hazard management. This proactive approach focuses on identifying and mitigating risks before they lead to incidents, marking a transformative change in safety management.
The advent of new technologies, like advanced data analytics and the Internet of Things (IoT), is reshaping OSHA compliance strategies. These tools offer real-time insights into workplace safety conditions, facilitating swift action to prevent hazards. They also streamline compliance processes, particularly in aspects like recordkeeping and incident reporting.
There’s also an increasing focus on cultivating comprehensive safety cultures within organizations. This holistic approach transcends basic regulatory adherence, promoting a work environment where safety is a core value and every employee plays a part in upholding it.
As OSHA compliance continues to evolve, it’s imperative for businesses to remain agile and informed, adapting their safety practices to align with the latest developments and best practices.